Drewniana maszyna parowa
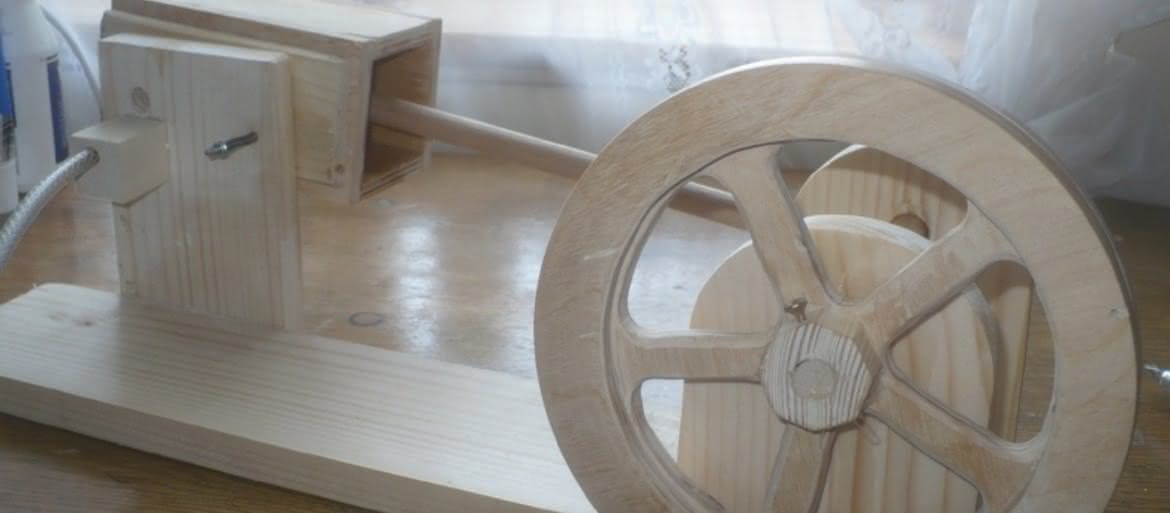
Prostota konstrukcji maszyny parowej z wahliwym cylindrem to jej wielka zaleta i możemy pokusić się, aby taki model zrobić z drewna. Z pewnością chcielibyśmy, aby nasz model działał, a nie tylko stał. To jest do osiągnięcia. Napędzać go jednak będziemy nie gorącą parą, a zwykłym zimnym powietrzem, najlepiej z domowej sprężarki albo na przykład odkurzacza. Drewno jest ciekawym i łatwym w obróbce materiałem i dlatego można mechanizm maszyny parowej w nim odtworzyć. Ponieważ, budując nasz model, przewidzieliśmy boczną zdejmowaną część cylindra, dzięki temu możemy zobaczyć, jak pracuje tłok i jak przemieszcza się cylinder względem otworów rozrządu. Proponuję od razu zabierać się do pracy.
Działanie maszyny parowej z wahliwym cylindrem. Możemy je przeanalizować na fotografii 1 na serii zdjęć oznaczonych od a do f.
- Do cylindra poprzez otwór wlotowy dostaje się para, która popycha tłok.
- Tłok poprzez tłoczysko i korbę korbowodu obraca koło zamachowe.
- Cylinder zmienia swoje położenie, w miarę przesuwania się tłoka zasłania otwór wlotowy i odsłania otwór wylotowy pary.
- Tłok poruszany bezwładnością rozpędzonego koła zamachowego wypycha zużytą parę przez ten otwór i cykl rozpoczyna się od początku.
- Cylinder zmienia pozycję i otwór wlotowy zostaje odsłonięty.
- Sprężona para znowu wpływa przez otwór wlotowy i popycha tłok.
Narzędzia: wiertarka elektryczna na statywie, wiertarka zamocowana do stołu warsztatowego, szlifierka taśmowa, szlifierka wibracyjna, dremel z końcówkami do obrabiania drewna, wyrzynarka, glutownica z klejem na gorąco, narzynka M3 z uchwytem do gwintowania, wiertło stolarskie 14 milimetrów. Do napędu modelu zastosujemy sprężarkę albo odkurzacz.
Materiały: deska sosnowa o szerokości 100 i grubości 20 milimetrów, wałek o średnicy 14 milimetrów, listwa 20 na 20 milimetrów, listwa 30 na 30 milimetrów, listwa 60 na 8 milimetrów, sklejka o grubości 10 milimetrów. Smar silikonowy albo oliwa do maszyn, gwóźdź o średnicy 3 milimetrów i długości 60 milimetrów, mocna sprężynka, nakrętka z podkładką M3. Lakier bezbarwny w aerozolu do polakierowania drewna.
Podstawa maszyny. Zrobimy ją z deski o wymiarach 500 na 100 na 20 milimetrów. Dobrze jest przed polakierowaniem wyrównać papierem ściernym wszystkie nierówności deski i miejsca po cięciu.
Suport koła zamachowego. Wytniemy go z deseczki sosnowej o wymiarach 150 na 100 na 20 milimetrów. Potrzebujemy dwóch jednakowych elementów. Po zaokrągleniu szlifierką taśmową, z założonym papierem ściernym 40, górnych krawędzi w łuki i obrobieniu papierem ściernym drobnym w suportach wiercimy otwory o średnicy 14 milimetrów w miejscach jak na zdjęciu 2. Wysokość suportu na odcinku między podstawą i osią ma być większa niż promień koła zamachowego.
Wieniec koła zamachowego. Wytniemy go ze sklejki o grubości 10 milimetrów. Koło ma średnicę 180 milimetrów. Na sklejce narysujemy cyrklem dwa jednakowe koła i wytniemy je wyrzynarką. Na pierwszym kole współosiowo narysujemy koło o średnicy 130 milimetrów i wytniemy jego środek. To będzie wieniec koła zamachowego, czyli jego obrzeże. Wieniec ma zwiększać bezwładność obracającego się koła.
Koło zamachowe. Nasze koło zamachowe ma pięć szprych. Powstaną one w ten sposób, że na kole narysujemy pięć trójkątów z zaokrąglonymi brzegami i obróconych o 72 stopnie względem osi koła. Zaczniemy od narysowania koła o średnicy 120 milimetrów, a następne szprych o grubości 15 milimetrów i kółek w rogach powstałych trójkątów na papierze. Widać to na zdęciu 3. i 4., gdzie jest pokazana konstrukcja koła. Papier nakładamy na wycięte koła i punktakiem wyznaczamy środki wszystkich małych kółek. To zapewni precyzję wiercenia. Wszystkie rogi trójkątów przewiercamy wiertłem o średnicy 14 milimetrów. Ponieważ wiertło łopatkowe może strzępić sklejkę, dobrze jest wiercić tyko do połowy jej grubości, a następnie odwrócić materiał na drugą stronę i dopiero dokończyć wiercenie. Wiertło płaskie o tej średnicy zakończone jest maleńkim wystającym pilotem, który pozwoli nam bezbłędnie znaleźć środek wierconego otworu po drugiej stronie sklejki. Rozmyślając nad wyższością stolarskich wierteł cylindrycznych nad stolarskimi wiertłami płaskimi, wyrzynarką wytniemy pozostały zbędny materiał z koła zamachowego, aby uzyskać efektowne szprychy. Dremelem wyrównujemy wszelkie niedokładności oraz zaokrąglamy brzegi szprych. Koło sklejamy z wieńcem za pomocą kleju wikolowego. Centralnie wiercimy otwór o średnicy 6 milimetrów, aby w środku włożyć śrubę M6, uzyskamy w ten sposób prowizoryczną oś obrotu koła. Po zamocowaniu tejże śruby jako osi koła w wiertarce, obrabiamy szybko wirujące koło najpierw grubym, a potem drobnym papierem ściernym. Radzę zmienić kierunek obrotów wiertarki na taki, by śruba mocująca koło się nie luzowała. Koło powinno mieć gładkie brzegi a po obróbce obracać się równo bez bicia na boki. Gdy to uzyskamy, demontujemy prowizoryczną śrubę i rozwiercamy otwór na docelową oś do średnicy 14 milimetrów.
Korbowód. Wytniemy go ze sklejki o grubości 10 milimetrów. Dla ułatwienia pracy proponuję zacząć od wywiercenia dwóch otworów o średnicy 14 milimetrów w odległości 38 milimetrów od siebie, a dopiero potem wypiłować ostateczny klasyczny kształt jak na fotografii 5.
Oś koła zamachowego. Jest zrobiona z wałka o średnicy 14 milimetrów i ma 190 milimetrów długości.
Oś korbowodu. Jest odcięta z wałka o średnicy 14 milimetrów i ma 80 milimetrów długości.
Cylinder. Wytniemy go ze sklejki o grubości 10 milimetrów. Składa się z pięciu elementów. Dwa z nich mają wymiary 140 na 60 milimetrów i są to boczne ścianki cylindra. Denko i górna część mają wymiary 140 na 80 milimetrów. Dno cylindra ma wymiary 60 na 60 i 15 milimetrów grubości. Części te widoczne są na fotografii 6. Dno i boki cylindra sklejamy klejem wikolowym. Prostopadłość klejenia ścianek i dna jest jednym z warunków prawidłowej pracy modelu. W górnej części pokrywy cylindra wiercimy otworki na drewnowkręty. Otwory wiercimy wiertłem 3 milimetry, tak by trafiały w środek grubości ścianek cylindra. Otwory w pokrywie jeszcze lekko nawiercamy wiertłem 8 milimetrów, tak by łby śrub mogły się schować.
Tłok. Jego wymiary to 60 na 60 na 30 milimetrów. W tłoku wiercimy centralnie nieprzelotowy otwór średnicy 14 milimetrów na głębokość 20 milimetrów. Do niego wkleimy tłoczysko.
Tłoczysko. Jest zrobione z wałka o średnicy 14 milimetrów i ma 320 milimetrów długości. Tłoczysko jest z jednej strony zakończone tłokiem, a z drugiej chwytem osi korby korbowodu.
Chwyt osi korbowodu. Zrobimy go z klocka o przekroju 30 na 30 i długości 40 milimetrów. W klocku wiercimy przelotowo otwór 14 milimetrów i drugi nieprzelotowy prostopadły do niego. Do tego otworu wkleimy drugi wolny koniec tłoczyska. Wnętrze otworu przelotowego czyścimy i wygładzamy zwiniętym w rurkę papierem ściernym drobnym. W otworze będzie obracała się oś korbowodu i będzie nam zależało na zmniejszeniu w tym miejscu tarcia. Wreszcie uchwyt zaokrąglamy i kształtujemy za pomocą pilnika do drewna albo szlifierki taśmowej.
Suport rozrządu. Wytniemy go z deseczki sosnowej o wymiarach 150 na 100 na 20. Po obrobieniu papierem ściernym w suporcie wiercimy trzy otwory w miejscach jak na rysunku. Pierwszy to 3-milimetrowej średnicy otwór na oś rozrządu. Dwa pozostałe to otwór wlotowy i wylotowy powietrza do cylindra. Miejsce wywiercenia wszystkich trzech widać na zdjęciu 7. Jeśli zmieniamy wymiary części maszyny, należy miejsca wiercenia znaleźć eksperymentalnie, montując wstępnie maszynę i określając pozycję górną i dolną cylindra, a dokładnie miejsce, w którym znajduje się otwór wywiercony w cylindrze. Miejsce, gdzie będzie pracował rozrząd, szlifujemy szlifierką oscylacyjną z drobnym papierem. Ma być płaskie i bardzo gładkie.
Oś wahliwego rozrządu. Koniec gwoździa o długości 60 milimetrów tępimy i zaokrąglamy pilnikiem albo na szlifierce. Za pomocą narzynki M3 gwintujemy jego koniec na długości około 10 milimetrów. Do tego dobieramy mocną sprężynkę, nakrętkę M3 i taką podkładkę.
Rozrząd. Zrobimy go z listewki o wymiarach 140 na 60 na 8 milimetrów. W tej części modelu wiercimy dwa otwory. Pierwszy o średnicy 3 milimetrów. Umieścimy w nim gwóźdź, będący osią obrotu cylindra. Pamiętajmy o takim nawierceniu tego otworu, by łepek gwoździa był dokładnie zagłębiony w drewnie i nie wystawał ponad jego płaszczyznę. To bardzo istotny moment naszej pracy, wpływający na poprawne działanie modelu. Drugi otwór o średnicy 10 milimetrów to otwór wlotowo-wylotowy powietrza. W zależności od położenia cylindra względem otworów w suporcie rozrządu powietrze będzie dostawać się pod tłok, popychając go, a potem w kierunku przeciwnym będzie wypychane przez ten tłok. Rozrząd wraz z wklejonym gwoździem, pełniącym rolę osi, przyklejamy do powierzchni cylindra. Oś nie powinna się chwiać i ma być prostopadła do powierzchni. Wreszcie wiercimy otwór w cylindrze, posiłkując się położeniem otworu w deseczce rozrządu. Wszystkie nierówności drewna tam, gdzie będzie się stykać z suportem rozrządu, wygładzamy szlifierką oscylacyjną z drobnym papierem ściernym.
Montaż maszyny. Do podstawy przyklejamy suporty osi koła zamachowego, bacznie pilnując, by znalazły się w jednej linii i były równoległe do płaszczyzny podstawy. Przed całkowitym montażem pomalujmy elementy i zespoły maszyny lakierem bezbarwnym. Na oś koła zamachowego zakładamy korbowód i przyklejamy go do niej dokładnie prostopadle. Do drugiego otworu wklejamy oś korbowodu. Obie osie mają być do siebie równoległe. Do koła zamachowego przyklejamy drewniane pierścienie wzmacniające. W pierścieniu znajdującym się od zewnątrz umieszczamy w przewidzianym otworze drewnowkręt mocujący koło zamachowe na osi tego koła. Z drugiej strony podstawy przyklejamy suport cylindra. Wszystkie drewniane części, które będą się poruszać i ze sobą stykać, smarujemy smarem silikonowym lub oliwą do maszyn. Silikon należy lekko wypolerować, tak by dawał jak najmniejsze tarcie. Od tego będzie zależała prawidłowa praca maszyny. Cylinder montujemy na suporcie za pomocą jego osi wystającej z rozrządu. Widać to na zdjęciu 8. Na wystający poza suport gwóźdź nakładamy sprężynkę, potem podkładkę i całość zabezpieczamy nakrętką. Cylinder dociśnięty sprężynką powinien lekko poruszać się na swojej osi. Tłok wkładamy na jego miejsce do cylindra, a koniec tłoczyska nakładamy na oś korbowodu. Zakładamy wieczko cylindra i mocujemy je drewnowkrętami. Wszystkie współpracujące ze sobą części mechanizmu, a szczególnie cylinder i tłok, smarujemy oliwą maszynową. Nie żałujmy tłuszczu. Koło poruszone ręką powinno się obracać bez specjalnie wyczuwanych oporów, a korbowód ma przenosić ruch na tłok i cylinder. Fotografia 9. Do otworu wlotowego wkładamy koniec węża sprężarki i ją włączamy. Pokręćmy kołem, a sprężone powietrze poruszy tłok i koło zamachowe zacznie się obracać. Newralgicznym punktem w naszym modelu jest styk płytki rozrządu i jego stojana. Jeśli tamtędy nie ucieka większość powietrza, prawidłowo zrobiona maszyna powinna ruszyć bez problemu, dając majsterkowiczowi wiele radości. Powodem niesprawnego działania może być za słaba sprężynka. Po jakimś czasie oliwa wsiąka w drewno i tarcie staje się zbyt duże. To także niesie odpowiedź, dlaczego ludzie nie budowali maszyn parowych z drewna. Niemniej drewniana maszyna jest bardzo efektowna, a wiedza, jak działa wahliwy cylinder w takiej prostej maszynie parowej, zostaje na długo.